Powder coating is a durable final finish for a broad range of manufactured items made of fiberglass including boats and sports equipment. As with all finishes, the quality and durability of the outcome is determined by the preparation and surface application. As an alternative to liquid paint finishes, powder coatings are sprayed onto primed fiberglass parts with an electrostatic spray gun applicator and cured to harden the finish.
Items you will need
Primer product and dipping or spraying applicator
Electrostatic compressor spray gun for powder coat finish
Low-temp powder coat particles
Industrial oven large enough for the powder coat to cure
If the substrate surface to be powder coated is not smooth, it can be sanded or sandblasted and cleaned to achieve a smooth finish. Once smooth and ready for paint, the object must be primed and grounded to accept the electrostatically charged dry paint particles.
The most common primer for fiberglass when using a powder coat finish is some formulation of iodine solution applied thinly by spraying or dipping the object in it. The iodine mixture promotes conductivity so that the electrostatically charged powder coat particles will be uniformly attracted to the object or part being coated.
Once the primer is uniform and set, but not necessarily dry, the finish powder coat can be sprayed onto the object in multiple coats as needed to achieve desired texture and finish.
Once coated, the object is heat cured in an industrial ultraviolet or infrared oven at between 300 and 400 degrees Fahrenheit, according to particular powder coat manufacturers' instructions. Once cooled, the finish is hardened and more durable than a liquid paint finish.
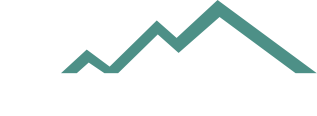