Boat flooring imparts many benefits to a boat's hull. The supporting framing and floor can add stiffness and support to a hull. The flooring creates a dead-air space just above the hull's bottom that can add bouyancy to a boat made from materials with no inherent bouyancy such as fiberglass, steel or aluminum. The floor provides support to additional deck equipment such and winches, consoles and seats. Flooring can provide added comfort by separating the occupants feet from bilge water and insulating the occupants from cold-water temperatures and the pumping action of the hull created when under way at high speeds.
Items you will need
Skilsaw
Table saw
Screw gun or drill motor with screw tip
Adhesive polyurethane caulk
Treated lumber
3/4-inch treated or marine plywood
Fiberglass resin
Fiberglass catalyst
Tape measure
Bevel square
Pencil
1/8-inch plywood
Acetone
Pilot drill
Fiberglass roller
Roller frame
Stainless steel screws
Framing
Cut a strip of 1/8-inch plywood 4 inches wide. Cut the factory edge from the sheet to insure that at least one edge is straight for use as a straightedge. Determine the desired height of the floor and subtract 1 1/2 inches from the height. Mark the inside of the hull at the bow and stern at this adjusted height. Connect these marks with the straightedge. This will be the top of the support cleats. Mark out both sides of the hull.
Hold a short straightedge from side to side (athwartships) between these marks on opposite sides. Lay the bevel square vertically onto the hull and the straightedge and tighten the nut on the square. Set up the tablesaw bevel angle as indicated by the square. Cut the support cleats on this angle. This will allow the cleats to project from the sides of the hull on a horizontal plane. Cleating should measure one and a half by one and a ahalf minus the bevel. Drill pilot holes about every 8 inches along the cleats. Apply a liberal bead of adhesive caulk onto the backside of the cleats. Immediately apply the cleats to the inside of the hull, dressing the top of the cleat to the line. Screw the cleats into the hull and allow the adhesive to cure fully 12 to24 hrs.
Measure from stem to stern along the cleats and mark out 16-inch intervals. This will indicate the deckbeam locations. Measure athwartships between these marks and cut 1 1/2 by 1 1/2 deckbeam material from the treated lumber. Crosscut the deckbeams at the athwartship measurements. Drill a pilot hole near the ends of the deckbeams where it laps over the cleats. Apply a dab of adhesive caulk at the lap and screw the beams down to the cleats. Cut additional cleat material and crosscut to act as a filler to fit between the beams to fully support the edges of the flooring.
Flooring
Measure the areas to be decked and cut the plywood to fit. Mix a batch of fiberglass resin with acetone to thin the resin to an almost watery consistency. Add the catalyst to the resin and immediately roll on a coat to both sides of the plywood and on all surfaces of the supporting framework. Allow the resin to soak into the wood and harden to provide additional waterproofing and stability to the materials.
Apply a heavy bead of adhesive caulk to the top edge of the cleats, beams and filler pieces. Immediately place the plywood pieces in position on the framing and screw the plywood down to the framing. Allow the adhesive to dry and trim off any adhesive squeezeout present above the flooring.
Caulk the edges of the flooring to the sides of the hull to provide a watertight seal and trap the air beneath to create the dead-air space. Allow the caulk to dry. Mix another thin batch of fiberglass resin and roll it onto the flooring to provide additional waterproofing and some impact resistance.
Warnings
- Use caution when using power tools, especially when cutting beveled pieces on the table saw. Loss of control over the material can result in the material binding between the blade, the rip fence and the saw deck and cause the material to be forcefully ejected toward your face and body potentially causing severe injury. Avoid contact between the resin and your skin. Immediately remove resin from skin using acetone and follow with warm water and mild soap.
Tips
- Mix small batches of resin at a time. High-air temperatures and direct sunlight can accelerate the chemical hardening reaction and drastically shorten working time.
Tips
- Mix small batches of resin at a time. High-air temperatures and direct sunlight can accelerate the chemical hardening reaction and drastically shorten working time.
Warnings
- Use caution when using power tools, especially when cutting beveled pieces on the table saw. Loss of control over the material can result in the material binding between the blade, the rip fence and the saw deck and cause the material to be forcefully ejected toward your face and body potentially causing severe injury. Avoid contact between the resin and your skin. Immediately remove resin from skin using acetone and follow with warm water and mild soap.
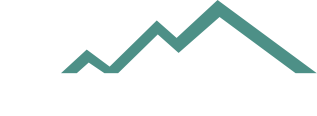