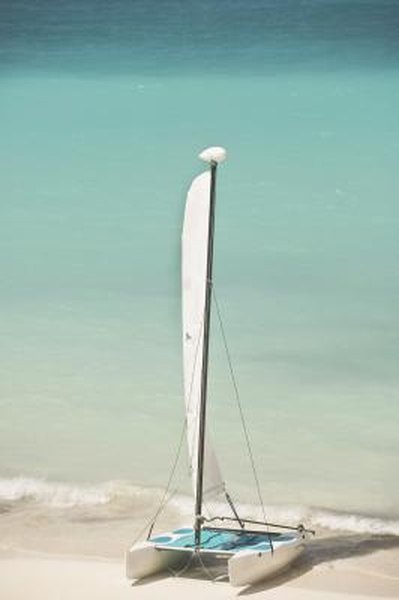
Pontoon boats have been around for decades. The design of these vessels allows for a large and bulky boat structure to be safely and easily supported by floating cylinders called pontoons. These boats have become very popular with families and fishermen alike because of their flat, walk-about decks and shaded canopies. Pontoon boats have either aluminum or fiberglass pontoons. While aluminum pontoons are air-filled, fiberglass pontoons are foam-filled. With the recent advent of creative material handling, the DIY boat builder can now produce safe, hand-laid fiberglass pontoons.
Items you will need
3/4-inch-by-4-foot-by-8-foot plywood
Tape measure
Chalk line
Circular saw
Framing square
3 sawhorses
Straightedge
Power drill
1/4-inch-by-2-inch galvanized wood screws
1/4-inch-by-1-inch galvanized wood screws
2-inch-by-12-inch-by-12-inch common lumber
Fiberglass-grade epoxy resin and hardener
Wooden or metal bucket
Fairing powder
Colloidal silica
Paintbrush
7.6-cm-by-3-inch fiberglass tape
Plastic-mesh scrubber
80-grit sandpaper
Drop cloth
Plastic bucket
4-pound/cf density closed-cell polyurethane foam
2-inch pine dowel
Construction glue
Fiberglass rollers
Build the Pontoon Frame
Step 1
Build a 3-foot-by-20-foot platform from 3/4-inch plywood and 2-inch-by-4-inch construction lumber using a tape measure and chalk line. Cut the platform with a circular saw and place it over three sawhorses. It will serve as both the work surface and the pattern holder of the pontoon design.
Step 2
From a point 12 inches from one end of the work surface, mark a spot 9 inches in from the edge and another identical spot on the other edge. This distance defines the width (18 inches) of the pontoon. Draw straight lines back from these points 18 feet in length, defining the length of the pontoon. Connect the front (bow) and back (transom) ends with squared lines.
Step 3
Use 3/4-inch plywood for the bottom (keel) and top (deck) and 1/2-inch plywood for the sides (hull). Measure 2 squared 18-inch-by-8-foot lengths of 3/4-inch plywood for the keel. Rip them with a circular saw. Lay them end to end -- beginning at the transom and going forward. (Note: this will leave a 2-foot space at the bow, so the deck will extend over the keel, producing a prow on the pontoon.) Measure and cut an 18-inch-by-12-inch piece of 3/4-inch plywood. Drill and screw it over the seam of the two keel pieces to attach them, forming the keel.
Step 4
Measure and cut 4 12-inch-by-8-foot lengths of 1/2-inch plywood. Connect these hull pieces at right angles to the keel, drilling 1/4-inch holes and driving 2-inch galvanized wood screws. The screws should be every 12 inches and 3/8-inch from the edge of the keel. Cut the 18-inch-by-12-inch transom and attach it to the hull pieces with 2-inch screws.
Step 5
Cut two 12-inch-by-24-inch-by-24 1/2-inch pieces of 1/2-inch plywood to form the triangular pieces of the prow hull. Measure and cut a 24 1/2-inch-by-12-inch piece of 1/2-inch plywood for the prow base. Screw the prow-hull and prow-base pieces together. Carefully invert the pontoon and attach the three-piece prow to the hull with 1-inch screws and scrap plywood on the inside of the hull. (Note that the add-on scrap pieces of plywood are necessary because there is no deck to attach them to at this point.)
Step 6
Measure and cut two 2-inch-by-12-inch-by-12-inch pieces of common lumber. They form the cross-members that span the sides of the hull. Place them at 64 inches and 128 inches down from the transom. Drill and drive 2-inch galvanized screws. Mark the outside of the hull at the center point of both cross-members.
Step 7
Mix one gallon of epoxy putty for sealing joints inside the pontoon hull. Mix the epoxy resin and hardener (2:1 ratio) in a wooden or metal bucket. Add equal parts of fairing powder and colloidal silica until it produces a peanut butter-like putty. Use a paint stirrer or epoxy stirrer to smooth the putty into joints and crevices inside the hull.
Step 8
Measure and cut 18-inch-by-12-inch lengths of 3/4-inch plywood to form the deck. Top drill and screw the deck to the hull with 2-inch screws. Drill five equidistant 2-inch holes down the center line of the deck, using a 4-inch hole-saw bit. Use a paintbrush to apply epoxy full strength to all seams on the pontoon. Allow the epoxy to dry for 2 hours and then cover all the seams and joint edges with 7.6-cm-by-3-inch fiberglass tape.
Fill and Glass the Pontoon
Step 1
Cover the deck with a drop cloth that leaves a 1-foot gap down the deck for hull protection. Use a plastic bucket to mix 10 gallons of 4-pound/cf density, closed-cell polyurethane foam -- in equal parts A and B. Mix 2 gallons at a time. Pour the mixed foam liquid into the deck holes -- two gallons into each hole, one at at time. Continue to fill the holes until expanded foam leaks out of the holes. Scrape and wipe between pourings to keep the deck clean. Allow the foam to cure overnight. Cut five 2-inch pieces of wood dowel. Glue them into the five foam holes with construction glue and sand them flat.
Step 2
Use a plastic mesh scrubber and water to remove the amine blush (a waxy byproduct of epoxy resin) from all taped seams. Sand the taped seams with 80-grit sandpaper. Invert the pontoon deck side down.
Step 3
Mix 2 gallons of epoxy resin and hardener (2:1 ratio). Use a fiberglass roller to roll on three coats of epoxy resin mixture over the entire hull, prow and transom. Cure the resin for 24 hours.
Step 4
Use lacquer thinner and a cloth to clean the epoxy surface. Mix more epoxy resin/hardener and use a roller to apply a thick coat to the entire hull, prow and transom. Drape the fiberglass fabric over the hull with the weave parallel to the keel. Use another clean roller to fix the fabric to the wet surface. After setting for three hours, trim the excess fiberglass cloth and paintbrush the edges and seams with more epoxy resin mixture. Repeat the scrub-wet-drape-roll-trim-edge process two more times over 48 hours.
Step 5
Invert the pontoon and repeat the glassing process on the deck.
Step 6
Sand the entire pontoon and -- if desired -- apply marine-grade paint in two coats.
References
- "The Fiberglass Repair and Construction Handbook"; Jack Wiley; 1998
Writer Bio
James Roberts began writing professionally in 1989, focusing initially on methodologies, multimedia courses and how-to articles on information technology, business, software, health care and relationships. His published works appear on various online article databases and he holds a Bachelor of Science in business from West Virginia University.
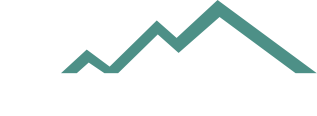