Lead works well for many do-it-yourself projects, primarily because of its low melting temperature, easy availability and low price. Thus collectors, craftsmen and fishermen are just some of the people that utilize the casting of lead to fabricate items. If you need to fabricate a custom item, consider making your own lead mold for the job.
Items you will need
Polymer clay
Petroleum jelly
Small aluminum pie pan
Plaster of Paris
Sealant
Paintbrush
Electric drill
Putty knife
Step 1
Craft a model out of polymer clay in the shape of the item for which you wish to make a mold. Follow the clay manufacturer's instructions for baking the clay hard. Allow the model to cool, then apply a coat of sealant with a paintbrush. Let it dry completely.
Step 2
Cover the model in a thin layer of petroleum jelly. Choose an aluminum pan large enough to hold your clay model easily and deep enough so that the model can be covered completely in plaster. Mix up enough plaster to fill the pan half-full and pour it into the pan.
Step 3
Set the clay model into the plaster and press on it slightly so that it submerges in the plaster only half-way. Allow the plaster to harden fully around the model. Apply a thin coat of petroleum jelly all over the now-dry plaster.
Step 4
Make another batch of plaster (enough to finish filling the pan and cover the model), and pour it on top of the petroleum jelly-coated plaster in the pan. Cover the clay model completely, and allow this plaster to dry fully.
Step 5
Place one hand on the dry plaster, and with the other, gently turn over the pan so that the mold slides out into your hand. Insert the edge of a putty knife in between the two layers of plaster and gently pry them apart. Remove the clay model and set it aside. Finish the mold by brushing a coat of sealant on the inside of the mold cavities and letting it dry.
References
Writer Bio
Anthony Smith began writing for Demand Studios in May of 2009 and has since written over 1400 articles for them. He also writes for "The College Baseball Newsletter." He attended the University of New Mexico, and has more than 25 years of experience in the business world.
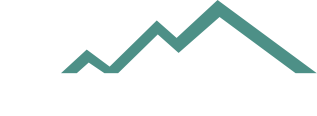